LayerZero's New In-House Powder Coating Line: A Strategic Step Toward Quality and Control
Watch a Video Tour of LayerZero's Paint Line
At LayerZero Power Systems, every decision is made with one purpose in mind: reliability. Whether it’s designing the next generation of Static Transfer Switches or refining the manufacturing process, the company is always focused on improving speed, quality, and performance. A recent investment in a fully automated in-house powder coating line marks a new chapter in LayerZero’s production capabilities, enhancing finish quality, turnaround speed, and production flexibility.
Built In-House, Designed for Precision
LayerZero’s new powder coating line was developed entirely in-house by the company’s fabrication and engineering teams. By integrating this process under one roof, LayerZero gains full control over coating quality, scheduling, and inventory readiness, allowing finished parts to be staged up to four weeks in advance, keeping production flowing.
“Keeping everything in-house will allow for us to have a much more consistent product process,” said Justin Merkel, Fabrication Lead at LayerZero Power Systems. “These are products that you will be able to install and that we can ensure won’t rust throughout its lifetime. That is what we are striving for, and it helps to create a better relationship between the company and its customers.”
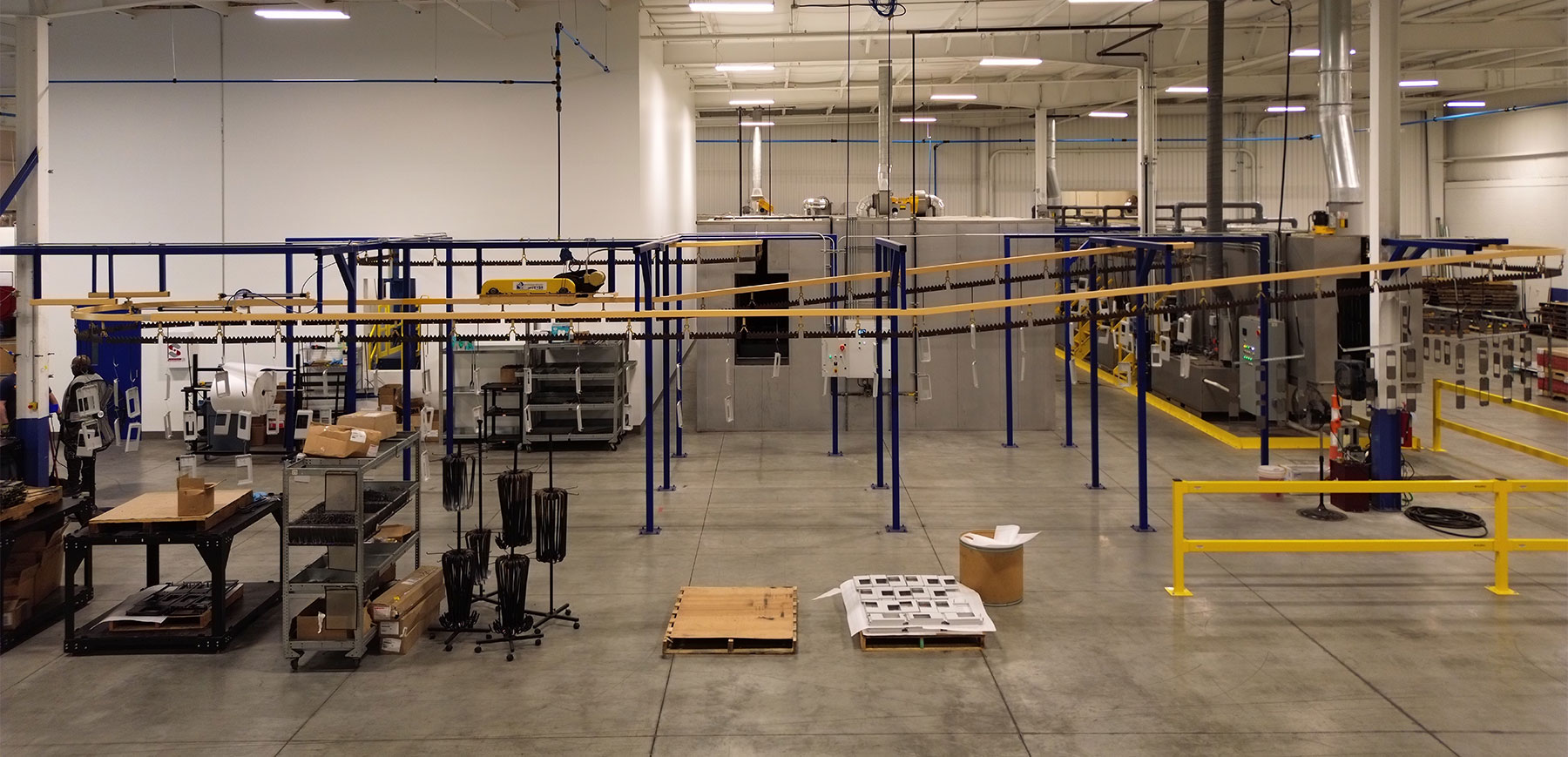
LayerZero's New In-House Paint Line
The Finishing Process, Step by Step
The paint line is designed for consistency, durability, and visual perfection. Every part passes through a multi-step finishing process that ensures strong adhesion, rust prevention, and a uniform, blemish-free appearance.
Here’s how the process works:
- Stage One: Alkaline cleaning removes oils and residues.
- Stage Two and Three: Dual rinse cycles ensure cleanliness.
- Stage Four: Zirconium conversion coating boosts adhesion and corrosion resistance.
- Dry-Off Oven: Prepares parts for coating.
- Nordson Paint Booth: Sensors detect part shape and orientation, triggering automated spray guns with Erie Powder.
- Cure Oven: Bakes parts for 16 minutes under 900°F panels.
- Final Inspection: Verifies thickness (minimum 2.8 mils) and visual quality.
“Every morning, and again before lunch, we verify the wash system to make sure the chemistry is spot-on,” said Steven Jagniszczak, Manufacturing Engineer at LayerZero Power Systems. “If anything’s off, the controller adjusts the chemical mix. It’s about the chemical mix. It’s about maintaining a consistent, high-quality finish.”
Calibrated for Quality
The Nordson paint booth is equipped with intelligent sensors that detect part size and orientation in real time. This data determines the exact position and timing for each spray gun, ensuring precise, even application across all geometries and part sizes.
The sensor technology inside the Nordson booth is one of Jagniszczak’s favorite features.
“There’s a big window the parts pass through, and sensors detect size, shape, and orientation,” he explains. “Based on that data, the spray guns know exactly when and how much to apply. It’s incredible tech.”
This automation minimizes waste, reduces touch-ups, and ensures uniform finish quality at scale.
What It Means for Customers
The benefits of the paint line go straight to LayerZero’s customers, including:
- Consistent Quality: Automated controls ensure every part meets strict visual and thickness standards.
- Stronger Inventory Readiness: With steel components painted and stocked in advance, final builds move more efficiently.
- Operational Flexibility: Internal coating capabilities allow for faster response to custom requirements.
“That’s the biggest customer win: quicker delivery,” said Jagniszczak. “They get the same high quality, just sooner.”
How the Community Can Help
While the paint line’s launch is the main story, a recent production focus on black finishes highlights how the new system enables quick adaptation to changing demand.
“About 95 percent of our units are black right now,” said Jagniszczak. “Gray is mostly for special orders or facility specs.”
Black finishes are easier to process in high volumes with exceptional consistency, enabling cleaner, more efficient runs. The result is a refined, uniform appearance that reinforces the high standards of quality and reliability customers have come to expect from LayerZero products.
What It Means for Customers
Bringing the powder coating line online took months of planning, testing, and refinement, a cross-disciplinary effort between LayerZero’s fabrication, engineering, and operations teams. From dialing in the spray patterns to perfecting the chemical balance in the wash system, every detail was carefully scrutinized to ensure repeatable, high-quality results.
“Seeing good parts come off the line is the most rewarding part,” said Jagniszczak. “It represents almost a year of work and sets us up for years of success.” The result is a smooth-running, precision-designed system capable of producing consistently finished parts with factory-grade efficiency and long-term reliability.
Quality, Layer by Layer
LayerZero’s new in-house powder coating line represents a strategic investment in quality, manufacturing efficiency, and long-term reliability. Our automated powder coating line is a powerful example of how operational innovation directly supports mission-critical reliability.
Because when uptime is mission-critical, every layer matters.
About LayerZero Power Systems
LayerZero Power Systems, based in Aurora, Ohio, is a leading manufacturer of mission-critical power distribution products under the LayerZero® brand. Founded in 2001, the company is committed to safety, reliability, and connectivity while making a positive impact in the communities it serves. By supporting initiatives like Fill a Bag, Feed a Family, LayerZero demonstrates its commitment not only to powering mission-critical infrastructure but also to empowering local
Learn more at LayerZero Power Systems.