Process Transparency at LayerZero
Lifecycle Management of Operations
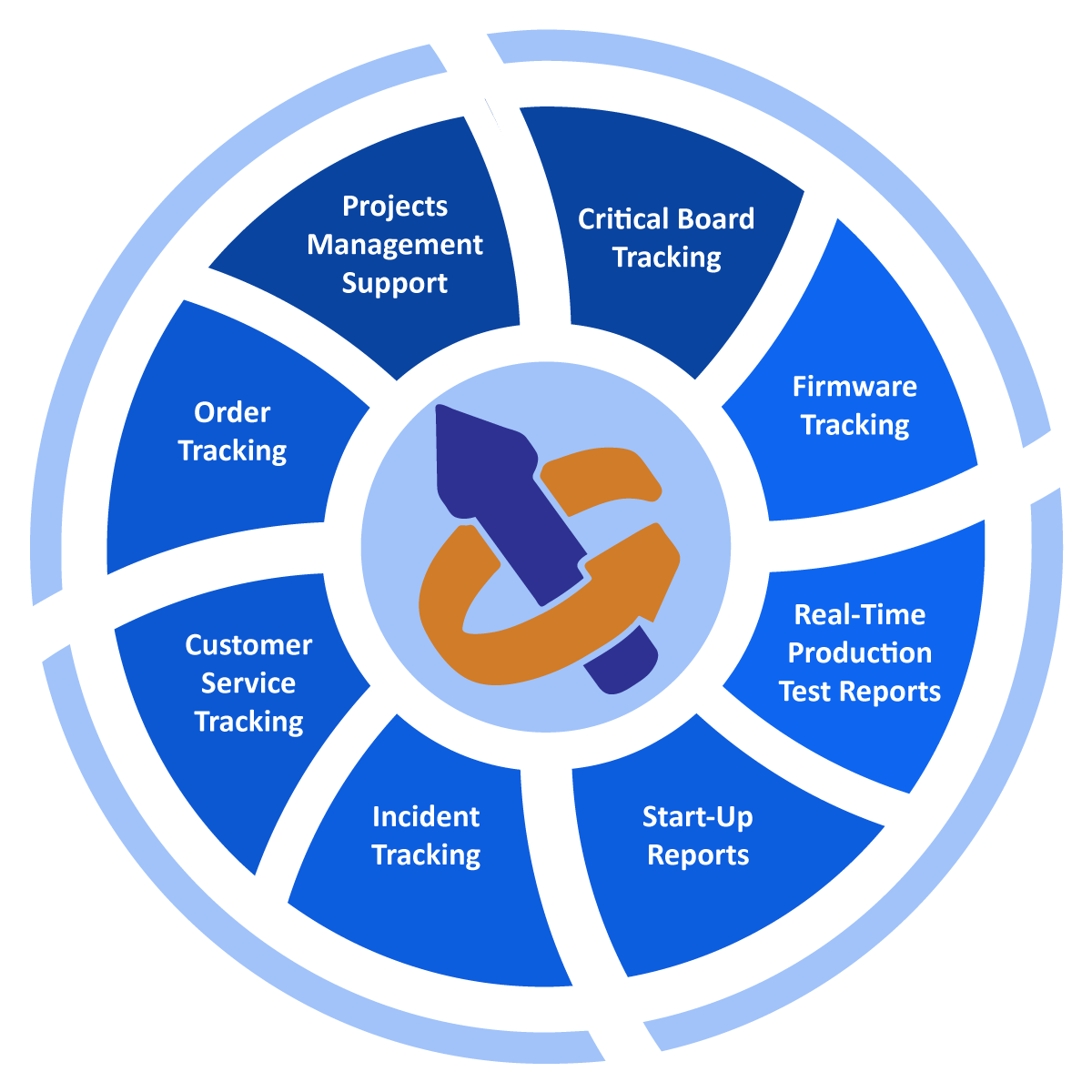
LayerZero Power Systems is dedicated to providing our customers with the highest level of service and support throughout the entire lifecycle of their power distribution systems. We offer comprehensive maintenance services and support for all our products, ensuring that your LayerZero power product operates at peak performance and reliability.
In addition, we provide ongoing training and support to our customers, equipping them with the knowledge and resources needed to effectively manage and maintain their LayerZero power products. Our goal is to deliver the utmost support and service, guaranteeing the long-term reliability and performance of their power distribution systems.
Quality Assurance
At LayerZero, quality is fundamental principle integrated into every aspect of our product development and manufacturing process. We take immense pride in conducting thorough testing throughout the manufacturing process, surpassing industry standards. Our comprehensive quality control system includes extensive testing, inspection, and auditing to ensure that every product leaving our facility is of the highest quality.
Our Manufacturing Process:
- Minimize defects
- Maintain consistent quality across all products
- Invest in advanced equipment and technology
- Improve accuracy, speed, and efficiency
- Uphold the highest quality standards
- Continuously review and enhance processes
LayerZero's Commitment to Quality:
- Conduct field tests to validate product performance
- Value customer feedback
- Leverage customer feedback to continually improve products and services
Order Tracking
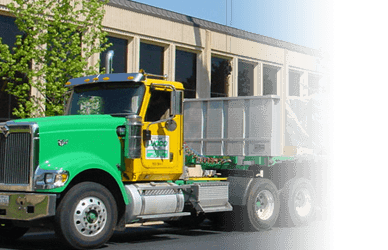
LayerZero's Order Tracking system ensures that customers can view real-time updates on the status of their products. You can monitor every stage, from receipt to production to shipping—delivering peace of mind and predictability.
A real-time production dashboard provides a visual representation of the build phase, factory staging, and expected delivery windows.
Firmware Tracking
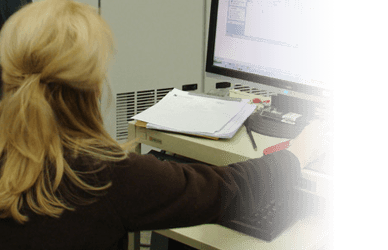
We maintain detailed firmware logs for every board we ship. Firmware Tracking ensures all critical components have traceable revision histories. Customers are informed of current versions and historical updates, giving full clarity into the software powering their systems.
These records are essential for diagnostics, future upgrades, and long-term reliability assurance.
Customer Service Tracking
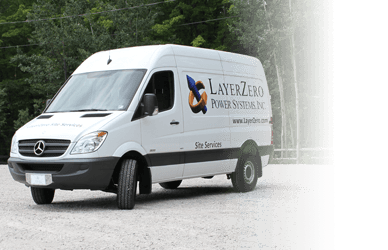
All service-related requests are tracked from creation through resolution. LayerZero's service portal links support tickets, status updates, and case documentation to your unit serial number, so we always know where things stand.
Our service team is equipped with a database of prior communication and component-level history for faster, more effective responses.
Incident Tracking
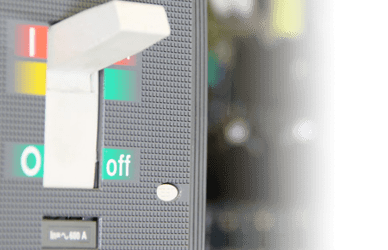
LayerZero uses a proactive approach to log, analyze, and resolve any internal or field-based incidents. Every report is reviewed and tied into continuous improvement workflows to ensure systemic issues are eliminated—not just patched.
This transparency fuels better engineering, safer products, and long-term trust.
Critical Board Tracking
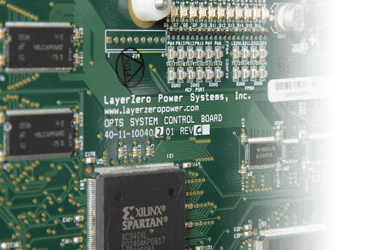
Every critical PCB in a LayerZero unit is serialized and logged into our database. Each board is traceable to its test reports, firmware versions, and incident records.
This enables total component-level accountability, providing visibility into component history long after shipment.
Real-Time Production Test Reports
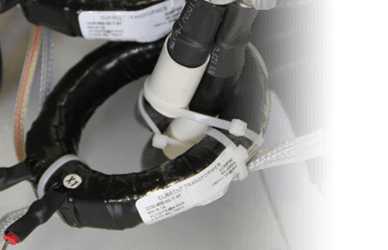
Before shipment, every unit undergoes a rigorous QA process—capturing load testing, signal integrity, fail-safe performance, and much more. Our systems automatically generate a real-time production test report which is stored and shared with customers.
This ensures that your LayerZero system was tested—and passed—under real-world simulated conditions.
Start-Up Reports
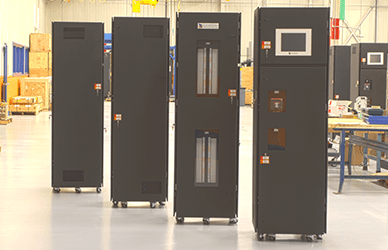
After installation, our service team performs a thorough start-up and commissioning process. Each item on the checklist is verified and recorded—including safety interlocks, voltage measurements, communication handshakes, and GUI responsiveness.
This report is archived under your system’s profile and used for future support and warranty reference.
Project Management Support
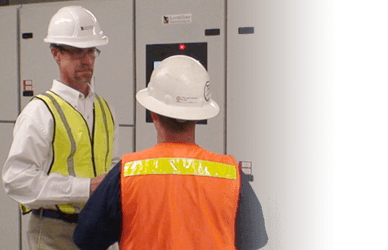
From PO to power-on, LayerZero assigns dedicated project management professionals to support each build. These team members coordinate milestones, manage documentation, ensure factory testing is on track, and maintain communication with customer-side PMs and engineers.
It’s a hands-on, human-driven support model that ensures your LayerZero experience is seamless.